We carry out any project that requires 3D Printing Technologies.
Comprehensive design: Our technical office will shape your product. We optimize aesthetics, facilitate manufacturing and improve the performance of the final product.
We can make an Optimized Design from your current design, we adapt the parts to the different 3D printing technologies, which leads to significant savings in material, delivery time and optimal mechanical characteristics.
Redesign and Scanning: Obtaining 3D files of a product for which we do not have drawings, as well as discontinued spare parts.
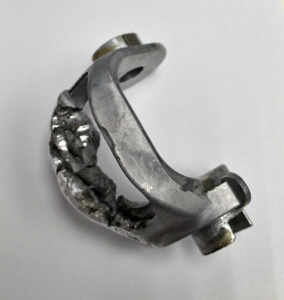
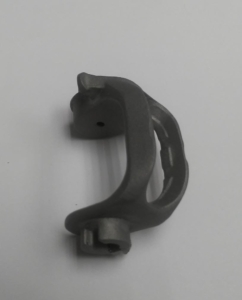
3D Printing Technologies at Traid Villarroya:
FDM (Fused Deposition Modeling):
FDM (Fused Deposition Modeling):
This is one of the most common 3D printing technologies. It works by extruding a molten plastic filament through a heated nozzle, which deposits the material layer by layer to build the object. It is widely used for prototypes and functional parts.
SLA (Stereolithography):
SLA (Stereolithography):
It is a 3D printing technology that uses a laser to cure liquid resin layer by layer. The laser selectively solidifies the resin based on the 3D design, producing parts with high precision and smooth surface finishes. It is ideal for applications requiring fine details.
SLS (Selective Laser Sintering):
SLS (Selective Laser Sintering):
It uses a laser to sinter (fuse) powder particles (usually plastic or metal) layer by layer to build an object. The laser selectively melts the powder based on the 3D design, creating strong, functional parts. It is suitable for prototyping and final part creation.
DMLS (Direct Metal Laser Sintering):
DMLS (Direct Metal Laser Sintering):
Similar to SLS, but specifically for metals, DMLS uses a high-powered laser to melt layers of fine metal powder, creating solid, detailed metal objects. This technology is used in the manufacturing of metal components in industries such as aerospace and medicine.
DLS (Digital Light Synthesis):
DLS (Digital Light Synthesis):
It is an advanced 3D printing technology that uses digital light (usually UV) to cure a liquid resin in a continuous and rapid process. Unlike SLA, DLS is capable of producing parts with better mechanical properties and at a higher speed. It is commonly used in industrial and consumer applications where high precision and durability are required.
COST REDUCTION
Compared to traditional production methods, 3D printing eliminates the need for expensive tooling, processes, and molds.
This means a lower cost of production, especially for small-quantity productions or custom parts.
COMPLEX PARTS
3D printing enables what is often difficult or even impossible to achieve with conventional methods.
Complex geometries and designs can be incorporated, optimised in such a way as to increase the efficiency and performance of the final products, as well as the printing of different elements on a single element.
FAST
3D printing builds the object layer by layer, adding material only where it is needed, significantly reducing production time.
It allows the production of multiple parts at once, reducing production time compared to traditional methods that usually work with a single part at a time.
The speed of manufacturing is very advantageous, allowing rapid iterations of parts and prototypes.
Traid Villarroya: Innovation and Quality at the Forefront of the Market
At Traid Villarroya, we are proud to be at the forefront of the market, which is why we offer a comprehensive and personalized service to each of our clients interested in additive manufacturing or 3D printing of both plastic and metal materials, through the use of different technologies by: filaments, resin, powder and laser sintering.
Always committed to offering quality and excellence in each project; We present ourselves as the ideal partner for those who are looking for a leading service in ambitious projects that seek innovation and precision in additive printing.
At Traid Villarroya we offer a new comprehensive service of 3D printing technology.
Contact us to request more information about our services.
We are members of the European Plastics Distributors Association (EPDA), The Performance Plastics Association (IAPD) and we actively collaborate with the Technological Institute of Plastics (AIMPLAS).